PROCESS
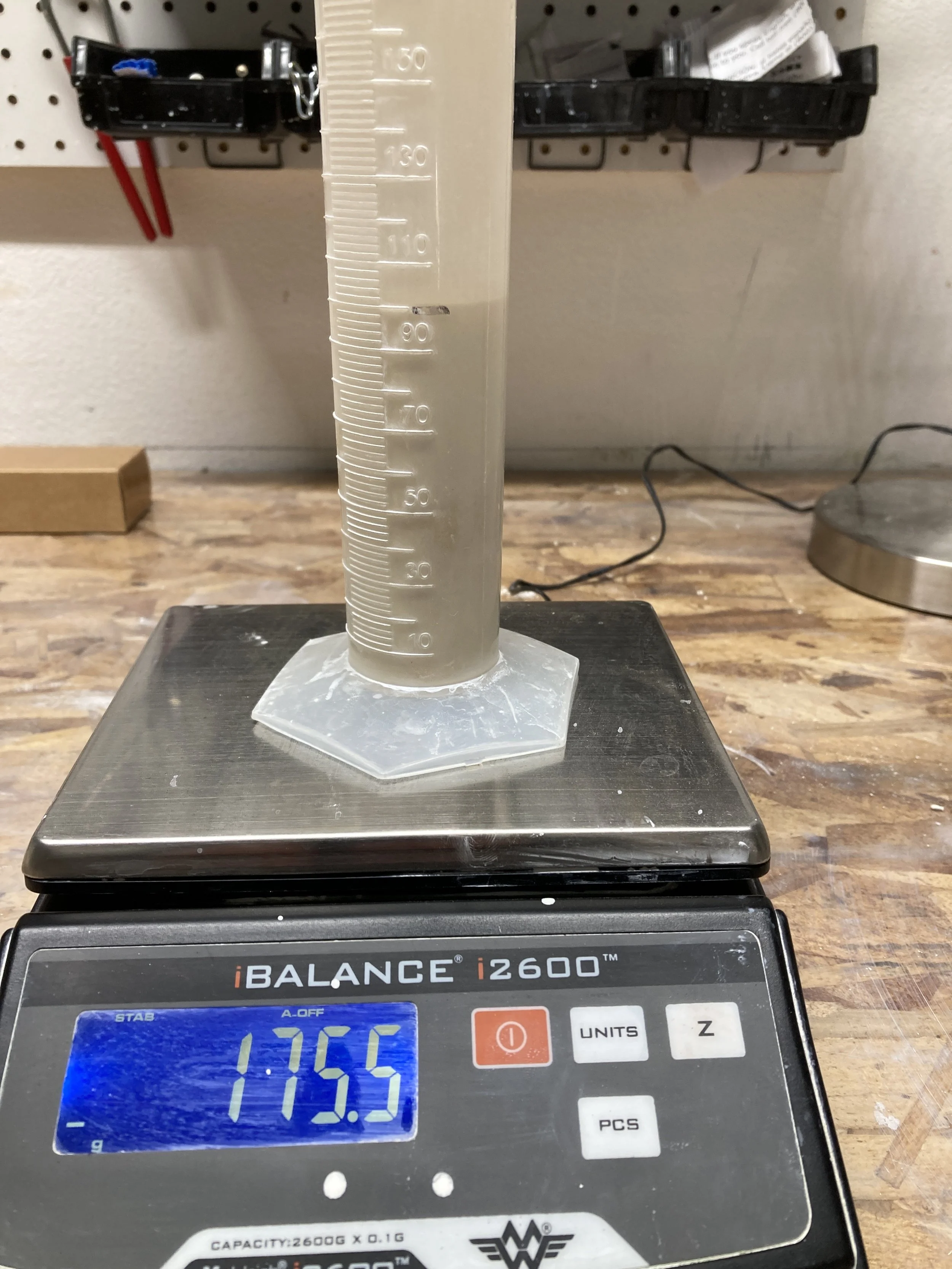
Adjusting slip to the proper specific gravity and viscosity makes casting a breeze. A sg much lower than this can introduce air bubbles, waterlogs the mold and increases casting time - all bad.

Slip filled to the brim. Folded paper and shims level out molds without a reservoir.
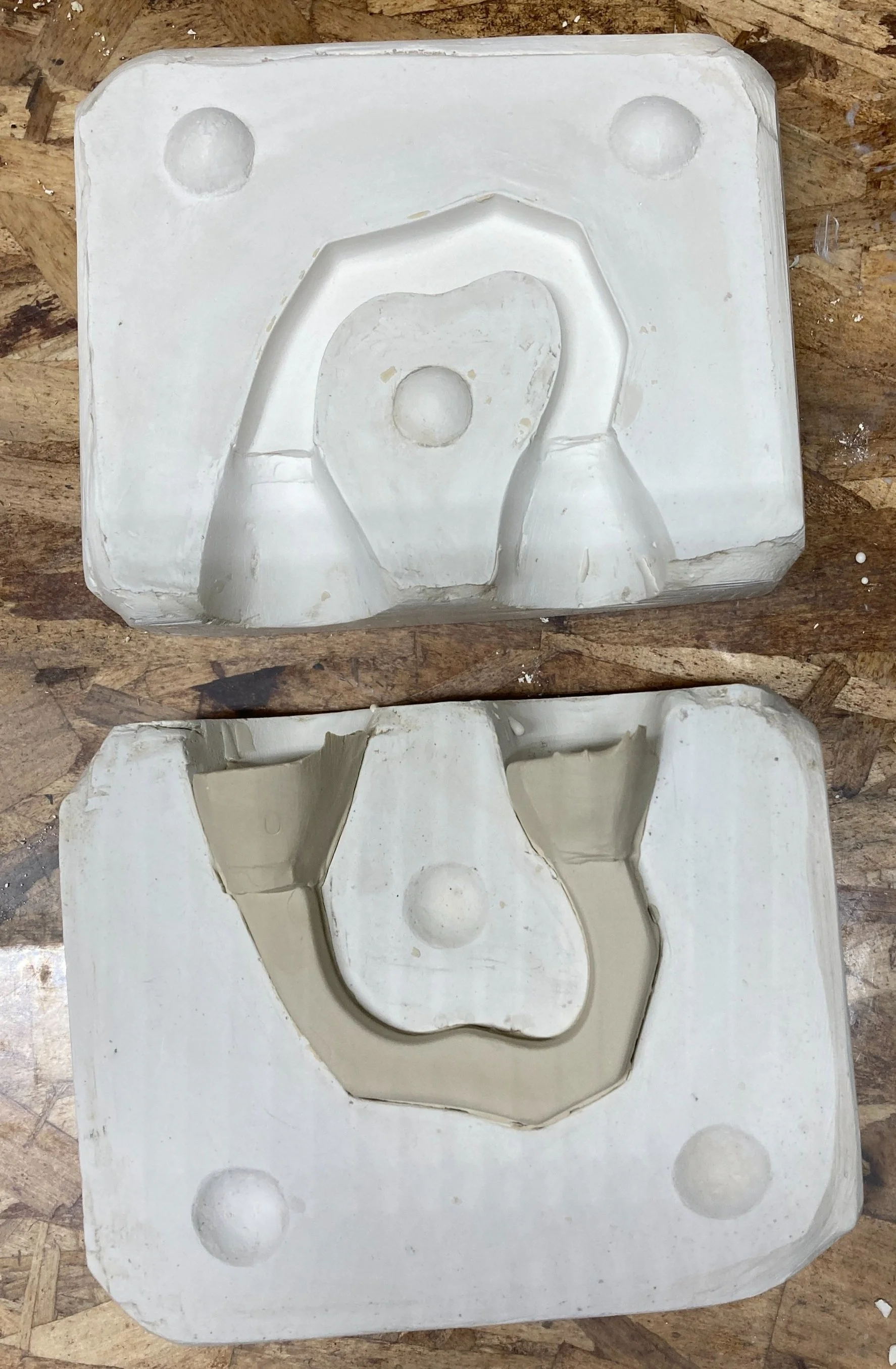
Two-part handle mold showing sprues to be trimmed.
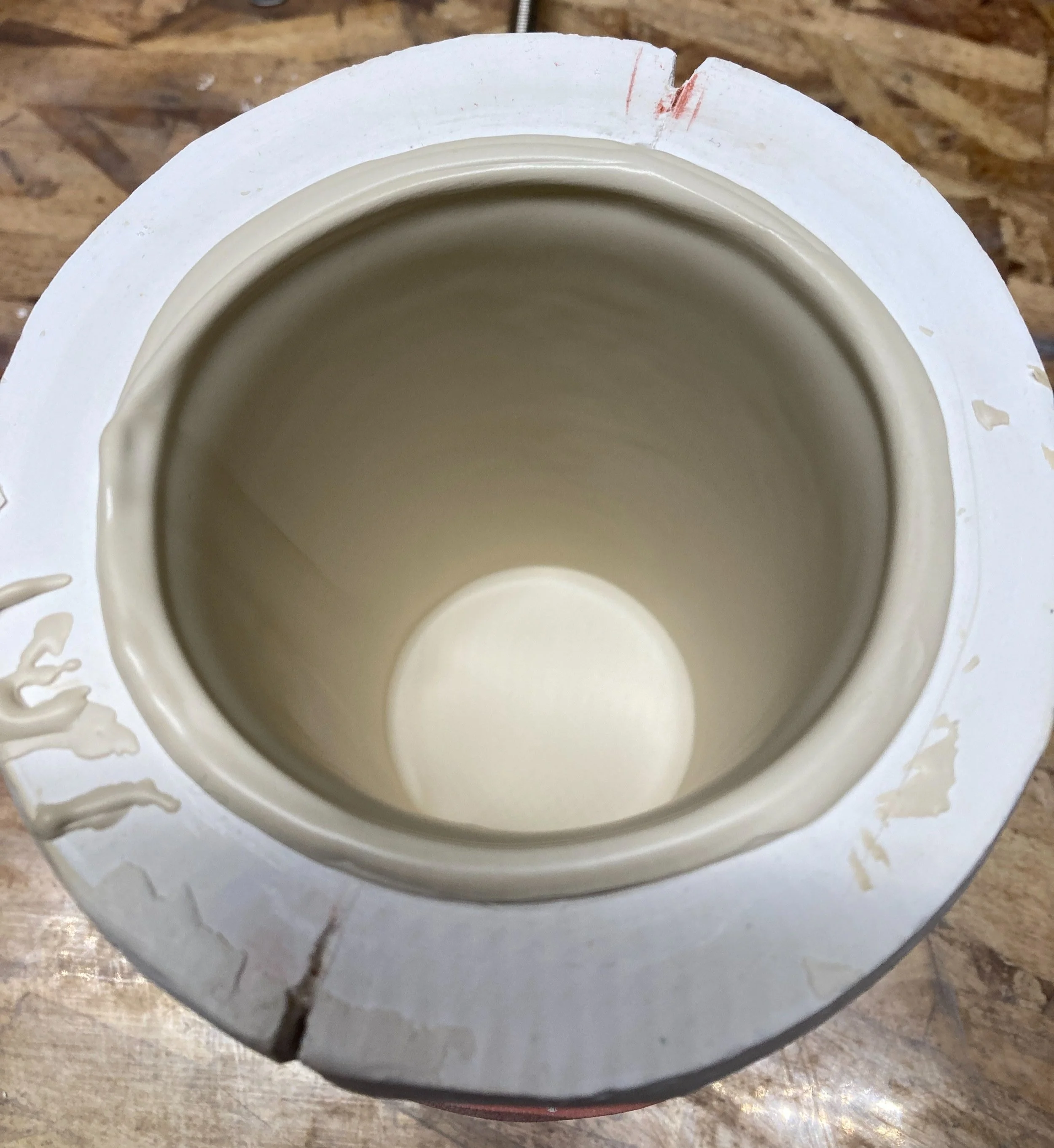
An example of a good slip cast interior. Even, no substantial drips. Casted in 13 minutes, no air bubbles, and ready for removal in 30 minutes. Along with specific gravity of slip, mold dryness, air temperature and humidity are factors in how an object casts.

A two-part crack mold. The positive form was made upside down on the wheel and then plaster poured while still on the wheel. You can see the saw marks on both sides where the flat blade scrapers and shims were inserted. A hammer is used to tap the handles of the paint scrapers to "crack" the mold open. A quicker process, but less durable molds that can chip easily. Surform shaver and sponge clean up the casting.
Slip cast porcelain handles are very easy to deal with. Scratch the attachment surfaces, dip surfaces in casting slip and stick on. I don't cover these, and they never crack. Fully dry in less than a day and ready to bisque fire. Also respond well to sponge clean.
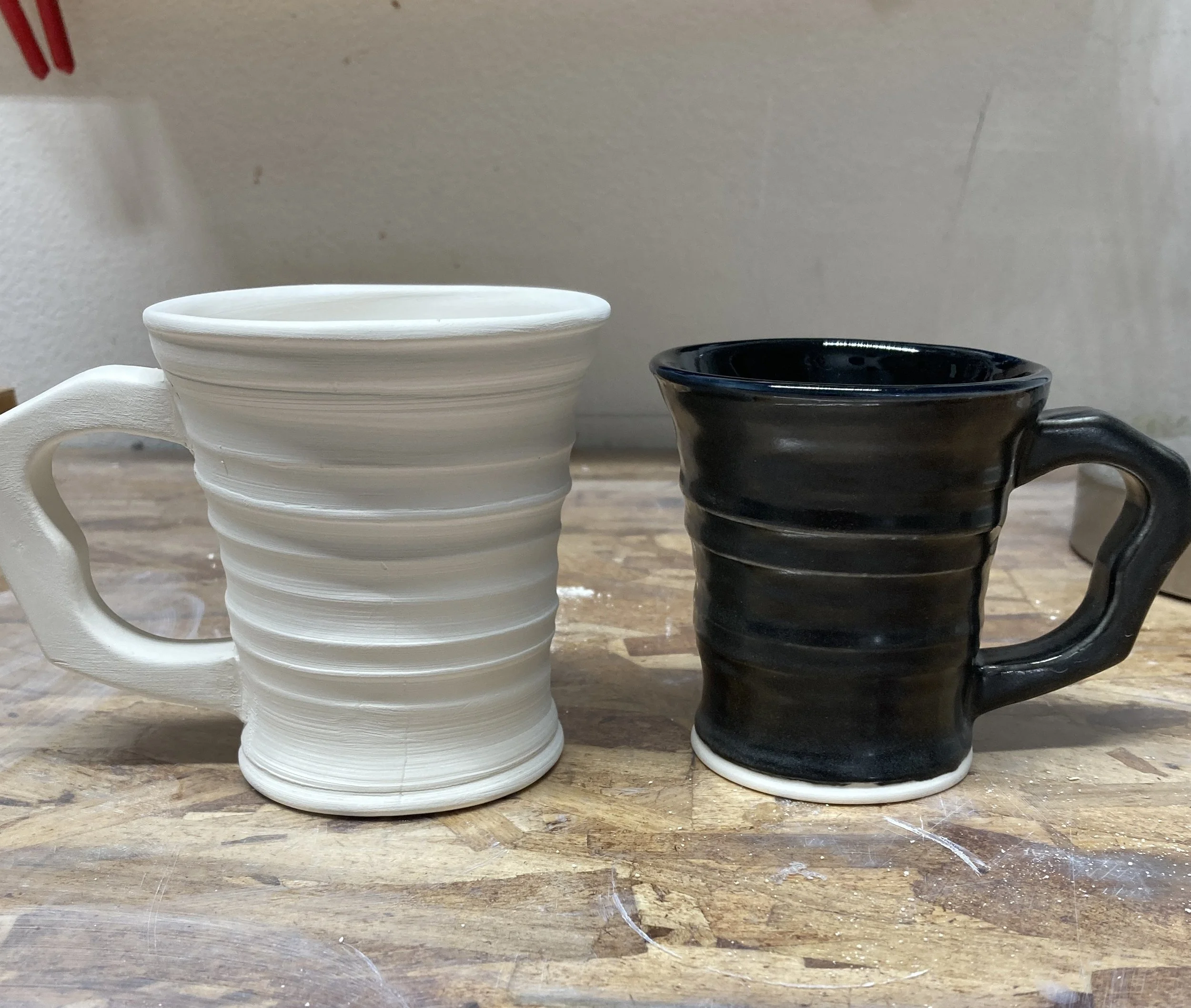
Greenware and final cup. Porcelain shrinks a lot!